Complying with OSHA bandsaw safety regulations
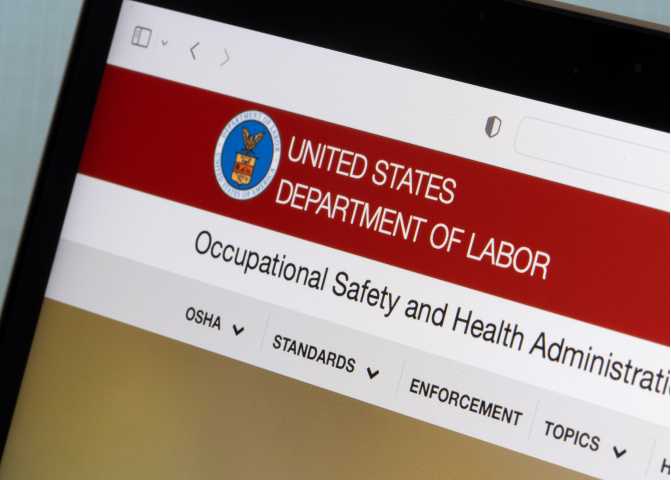
Dealing with the Occupational Safety and Health Administration (OSHA) is not something most employers want to avoid. It is often a costly and avoidable situation; however, bandsaws are dangerous pieces of equipment, and accidents inevitably happen. Therefore, it is essential to understand the regulations and procedures surrounding OSHA and bandsaw operation.
Bandsaw injuries reported to OSHA
In the United States, bandsaw injuries represent 11.5% of all OSHA-reported saw injuries from 1984-2017. In a 10-year period from 2007-2017, there were over 218 OSHA-reported injuries, specifically from meat bandsaws. Many of the bandsaw incidences reported to OSHA involved finger and hand lacerations, bruising, fractures, and in severe cases, amputation. However, there were probably countless other injuries that occurred; several studies suggest that between 20% to 70% of workplace injuries are underrecorded or not recorded at all.
The push from OSHA to reduce amputations
Due to the severity of workplace amputations, there is a nationwide drive led by OSHA to mitigate these incidents. OSHA introduced a National Emphasis Program (NEP) in late 2019, incorporating updated policies and procedures to reduce amputations within the manufacturing industries. It states that an entire master list of manufacturing establishments can be inspected in any order. Additionally, inspections conducted under this NEP can be combined with other programmed and unprogrammed inspections.
OSHA regulations and requirements with bandsaws
The OSHA has specific guidance on preventing injury when operating a bandsaw. Some items mentioned include machinery controls, operation instructions, protective equipment, and more. Here is a document OSHA created to help keep bandsaw operators safe. Generally speaking, OSHA will recommend that bandsaw-related businesses have more physical preventions in place so that an operator doesn’t come into contact with the blade. These may include blade guards, using blocks to push the material to the blade, or using blade-stopping technology.
OSHA standard 1910.212: Bandsaw machine guarding
OSHA Standard 1910.212 focuses on safeguarding employees from machine-related hazards, including bandsaws. In simple terms, this standard requires employers to provide effective guarding measures to protect workers from moving parts and other dangerous areas of bandsaws. These guards should be designed to minimize workers' exposure to the hazard zone while still allowing them to perform necessary tasks. By implementing the requirements of OSHA Standard 1910.212, employers can significantly reduce the chances of workers getting injured by bandsaws and ensure a safer working environment. The Guardian Bandsaw system for example, complies with this standard as it has an adjustable height blade guard in place.
Control of hazardous energy
CFR 1910.147
OSHA Standard 29 CFR 1910.147, commonly known as the Control of Hazardous Energy (Lockout/Tagout) standard, establishes requirements for the control of hazardous energy sources during servicing and maintenance of machines and equipment. This standard (which is currently being updated) aims to prevent unexpected startup or release of stored energy that could lead to serious injuries or fatalities. Bandsaws have moving parts, electrical systems, and potential energy stored in their components, such as tensioned blades or hydraulic systems. To ensure the safety of workers, the OSHA Lockout/Tagout standard requires proper isolation and de-energization of energy sources, such as shutting off power, releasing tension, and securely locking or tagging out equipment before performing maintenance or servicing tasks on bandsaws. Adhering to this standard helps mitigate the risks associated with unexpected startup or energy release, safeguarding workers from potential hazards while working with bandsaws.
ANSI Z244
It's also worthwhile considering ANSI Z244, which also focuses on the control of hazardous energy. The purpose of ANSI Z244 is to provide guidelines and establish best practices for the control of hazardous energy during servicing and maintenance activities on machines and equipment. Guardian Bandsaw will be able to create and provide proper documentation to control hazardous energy using 'alternative methods'.
Record keeping for bandsaw OSHA requirements
Record keeping and documentation are crucial aspects of OSHA compliance when it comes to bandsaw safety. Employers must maintain accurate and up-to-date records related to various aspects of bandsaw operations. This includes documentation of employee training on safe bandsaw operation, regular maintenance and inspection records, incident reports for any bandsaw-related injuries or accidents, and documentation of corrective actions taken. These records serve as evidence of the employer's commitment to safety and can be crucial during OSHA inspections or internal audits. Proper record-keeping helps demonstrate compliance with OSHA standards and enables employers to track trends, identify areas for improvement, and ensure ongoing adherence to safety protocols. It is essential to keep these records organized, accessible, and retained for the required duration to effectively manage bandsaw safety and maintain a safe working environment.
How to report a bandsaw injury to OSHA
If a severe bandsaw-related injury happens, you’re required to report the incident to OSHA within 8 to 24 hours. Failing to report the incident on time can result in fines as high as $13,260 per event.
Employers must report the incident by:
- In-person or phone call to the OSHA office closest to the location of the incident
- By phone to the OSHA toll-free line
- Or by submitting a form on the OSHA website
Some of the required information in each report includes:
- The business name
- The location of the work-related incident
- The time of the work-related incident
- Whether the incident involved a fatality, an in-patient hospitalization, an amputation, or an eye-loss
- The number of employees who suffered this type of injury
- The name(s) of the employee(s) who suffered the injury
- The name and phone number of the person to contact at the establishment; and
- A brief description of the incident.
What happens after you report a bandsaw-related incident with OSHA?
Once the report is submitted, an OSHA area director will decide which category the incident will fall into. There are three categories, generally based on the severity of the injury.
Category 1: usually the most serious of incidents that require an on-site inspection and can lead to a citation (these inform the employer of any regulations or standards that may have been violated along with any penalties or fines). An incident is classified as a Category 1 if the incident involves:
- Someone under the age of 18
- A fatality
- Incidences that involve two or more hospitalizations
- Repeat offenders
- The employer had similar incidences occurring within the past 12 months.
Category 2: Area Directors can determine if the incident requires a site visit or if a Rapid Response Investigation (RRI) can occur. These are usually less consequential and allow employers to self-investigate and make the necessary changes to prevent further incidents. With an RRI, the Area Director may make a phone call to gather any needed information about the incident.
Category 3: if the incident is deemed not to need an OSHA site visit, the employer can conduct their own RRI and make any required health and safety changes to their operation.
Losses from an OSHA inspection
Failing to meet basic safety standards can hurt businesses in more ways than one. When OSHA comes to inspect after an injury, there can be huge losses in production. Additionally, there’s the risk of further fines or citations on other pieces of equipment while the inspection takes place. The financial implications are serious. Many of the fines run into the thousands, with the maximum penalty for wilful or repeated violations being $145,000 per violation.
Although a different industry, there’s a great tool by the CDC which calculates the expected cost of injuries to a business. You can access that tool by clicking the button below.
Injury cost to business calculator
How Guardian Bandsaws help mitigate involvement from OSHA
Impressive 3D vision paired with powerful braking
The Guardian Bandsaw system incorporates cutting-edge safety features that could potentially save you the headache of an OSHA inspection. Our bandsaws use a high-speed camera vision system to detect operators’ blue or green gloves. The vision system creates a three-dimensioned area of safety surrounding the blade for the entire length of the blade. What sets our system apart is the use of four strategically placed cameras, generating a uniform rectangular vision zone that provides equal protection from the top to the bottom of the blade. By mounting the cameras to the frame, potential focusing issues are eliminated, guaranteeing optimal performance of our safety system. This patented vision system offers unparalleled protection and compliance, making Guardian Bandsaws the ideal choice for businesses.
In addition to the impressive 3-D vision, our braking system is another remarkable innovation that enhances safety and prevents accidents. Activating within milliseconds upon detecting an operator's blue or green glove, the braking system rapidly releases stored energy from a spring to clamp the blade, bringing it to a complete stop. This instantaneous response minimizes damage to the bandsaw and preserves the blade's integrity and sharpness for multiple activations. The braking system is designed to be highly efficient and reliable, requiring a simple push of a button to reset and resume operation, ensuring seamless workflow and productivity.
Better reporting and documentation
One other notable advantage of choosing Guardian Bandsaw is the comprehensive web portal for record-keeping and documentation. This platform allows businesses to track and manage all incidents and related information efficiently. By using the Guardian Bandsaw web portal, companies can maintain accurate records of bandsaw-related incidents, including details such as date, time, location, and nature of the incident. This centralized system streamlines the documentation process, ensuring that all necessary information is recorded promptly and securely.
In addition to incident tracking, the Guardian Bandsaw web portal enables businesses to generate comprehensive reports and analytics. These reports provide valuable insights into safety trends, identifying potential areas for improvement and helping businesses proactively address safety concerns.
What makes Guardian the safest bandsaw in the world
Perhaps it’s time to consider adding safety bandsaws to your production line. It’s better to improve workplace safety rather than run the risk of injury and potential OSHA investigation. When it comes to injury prevention and reducing OSHA interference, you can rely on Guardian Bandsaws. Our customers have reported zero injuries since adding our safety bandsaws to their production line. We can help you select the model that best suits your needs, so don’t hesitate to contact us.