5 ways to improve bandsaw safety
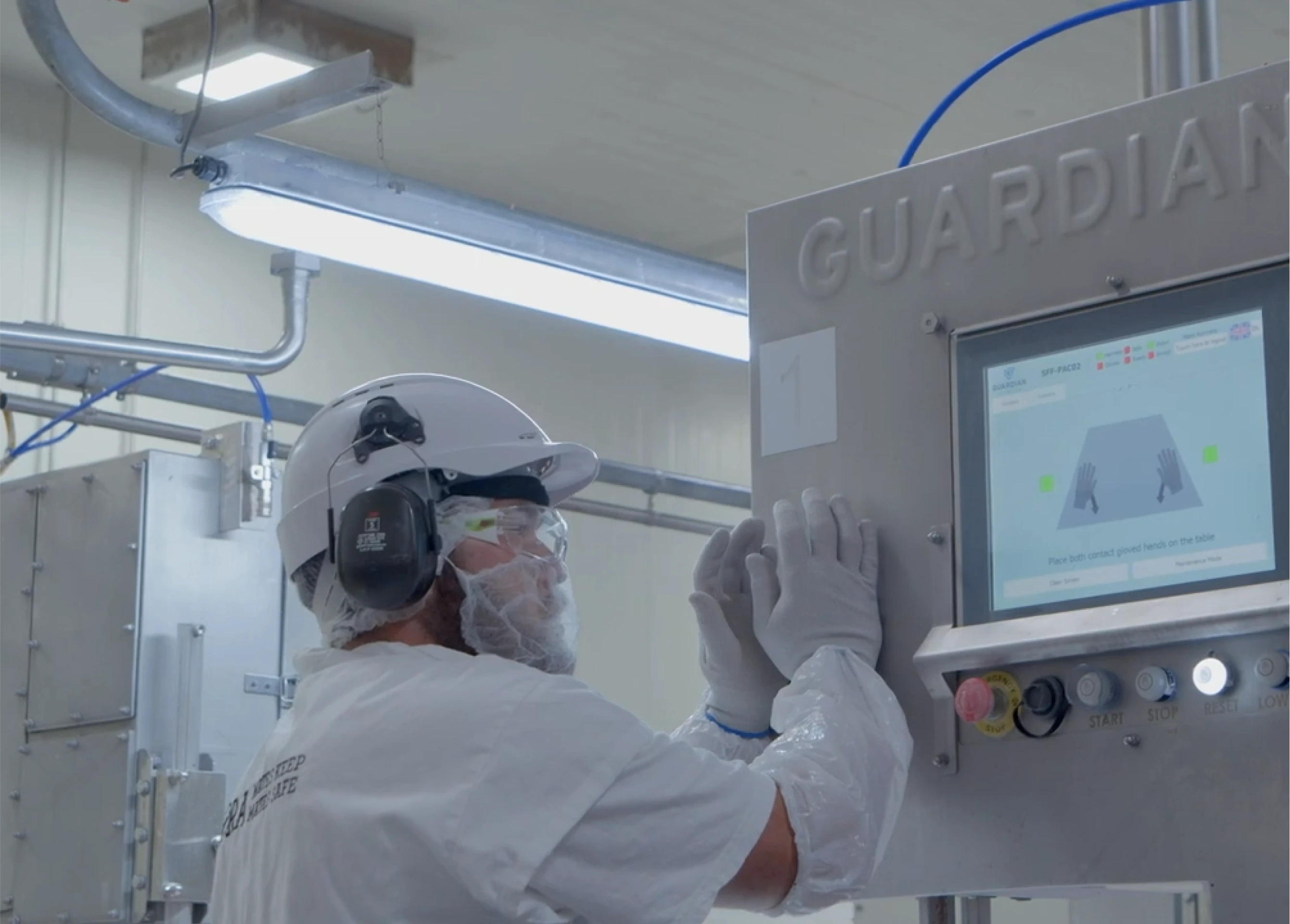
Improving bandsaw safety for your plant is one of the best ways to retain operators, increase productivity, and ultimately your profit margin. But with so many moving parts at play, what are some of the best ways to do this? At Guardian, we built our bandsaws with a safety-first approach - so here are some of our top tips to improve safety with your bandsaws and bandsaw operators.
1. Invest in ongoing training and supervision
Safety generally starts with the operator. Ensure that your team has a solid safety system in place, and make sure everyone understands it. It may even make sense to translate your system into multiple languages. In the United States alone, roughly 13% of bandsaw operators are of Latin or Hispanic descent, so providing these systems in their first language would be ideal. By addressing the essential health and safety concerns for every person, you reduce the chance of miscommunication, potential injury, and prosecution.
2. Use the right PPE
When operating a bandsaw, there are some basic PPE items that should always be worn to prevent injury. These include (but are not limited to):
- Safety glasses
- Hair tied back or in a net
- Wearing sturdy, enclosed footwear
- Hearing protection
- A hard hat
- And if required, a dust mask
It’s also important to be mindful of removing items like jewelry or loose clothing, as these can easily get caught in the blade and lead to serious injury.
3. Check bandsaw blades thoroughly and regularly
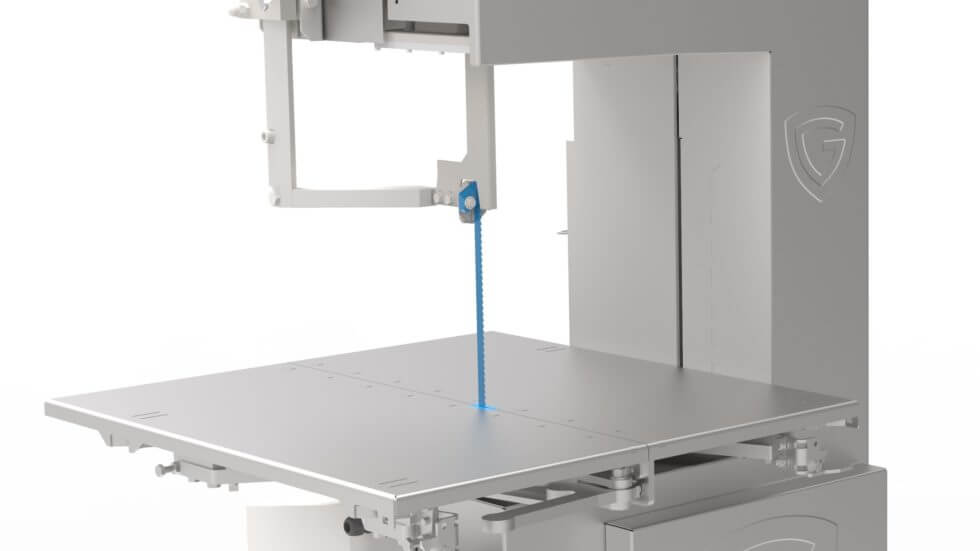
The bandsaw blades should be sharp, properly tensioned, and have no missing teeth. If the blade isn’t sharp enough there may be more resistance and kick-back to the operator. Similarly, blades that have missing teeth run the risk of not cutting through the material properly and instead catching on the material.
With Guardian, however, new blades are never far away. We offer same-day dispatch for all consumable parts orders, so you never have to worry about having inadequate blades again.
4. Vision sensing and blade-stopping technology
Many bandsaws are now fitted with cameras or infrared technology to detect if an operator gets too close to a blade. It’s one of the most effective ways to prevent a close-call injury. The Guardian high-speed vision system protects the operator by looking 360 degrees around the blade. As soon as a blue glove moves within the 40mm zone of the blade, the vision system picks up that part of the hand and within milliseconds the blade is de-tensioned and stopped. The operator then realizes they’ve made a mistake, presses the reset button, and resumes production.
https://www.youtube.com/watch?v=bYkV2O8iJiI
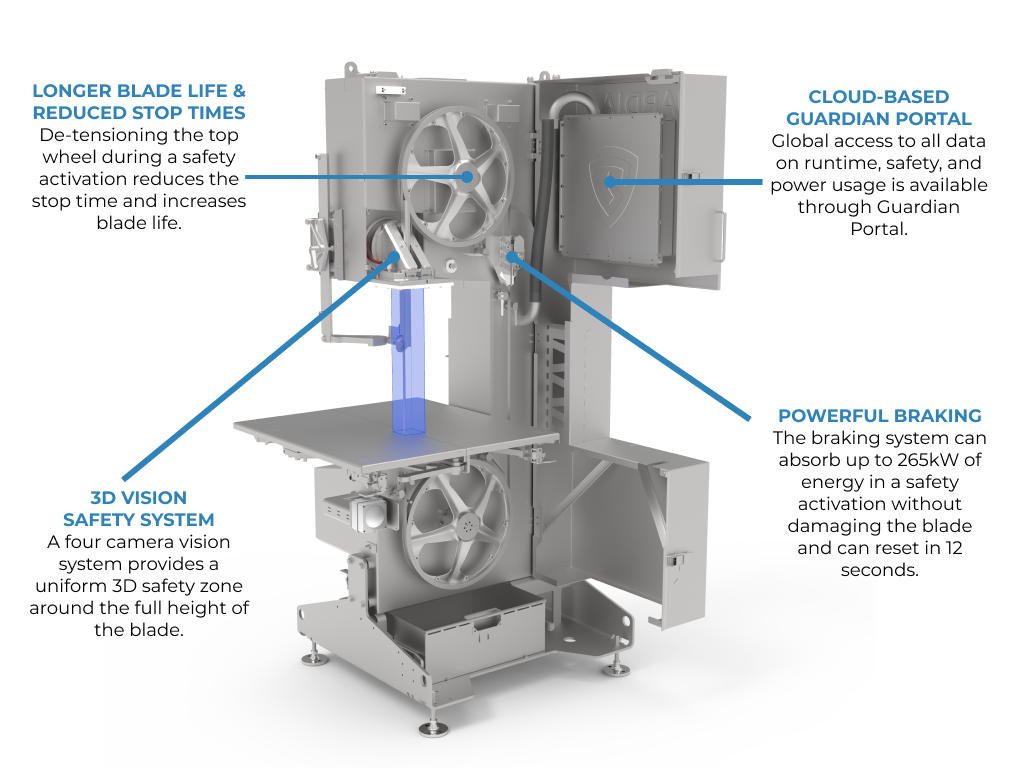
5. Software and data
A new element to consider is safety management software. In fact, this is now regarded as the most influential injury prevention method in the long term. The Guardian management software is an industry first and sets a new benchmark for safety performance reporting on band saws. Staff are able to log into the software from anywhere in the world and access a comprehensive suite of reports and charts showing the performance of the band saw and the interactions between staff during shifts.
The software is simple to use and powerful in creating meaningful reports that can help change behavior and improve safety and training systems. All activations are recorded so that any incidences can be dealt with swiftly. With data, you’ll be able to see the patterns, perhaps there’s a particular time of the day or time in the month when injuries most commonly occur. With this information, you’ll be better equipped to prevent that injury by staffing or monitoring accordingly.
When it comes to band saws, safety is paramount. Increasing your awareness of the above strategies could save you and your staff from serious injury and consequences for your business.
For more information about the Guardian system, feel free to get in touch with our team.