Steps to improve bandsaw operator retention
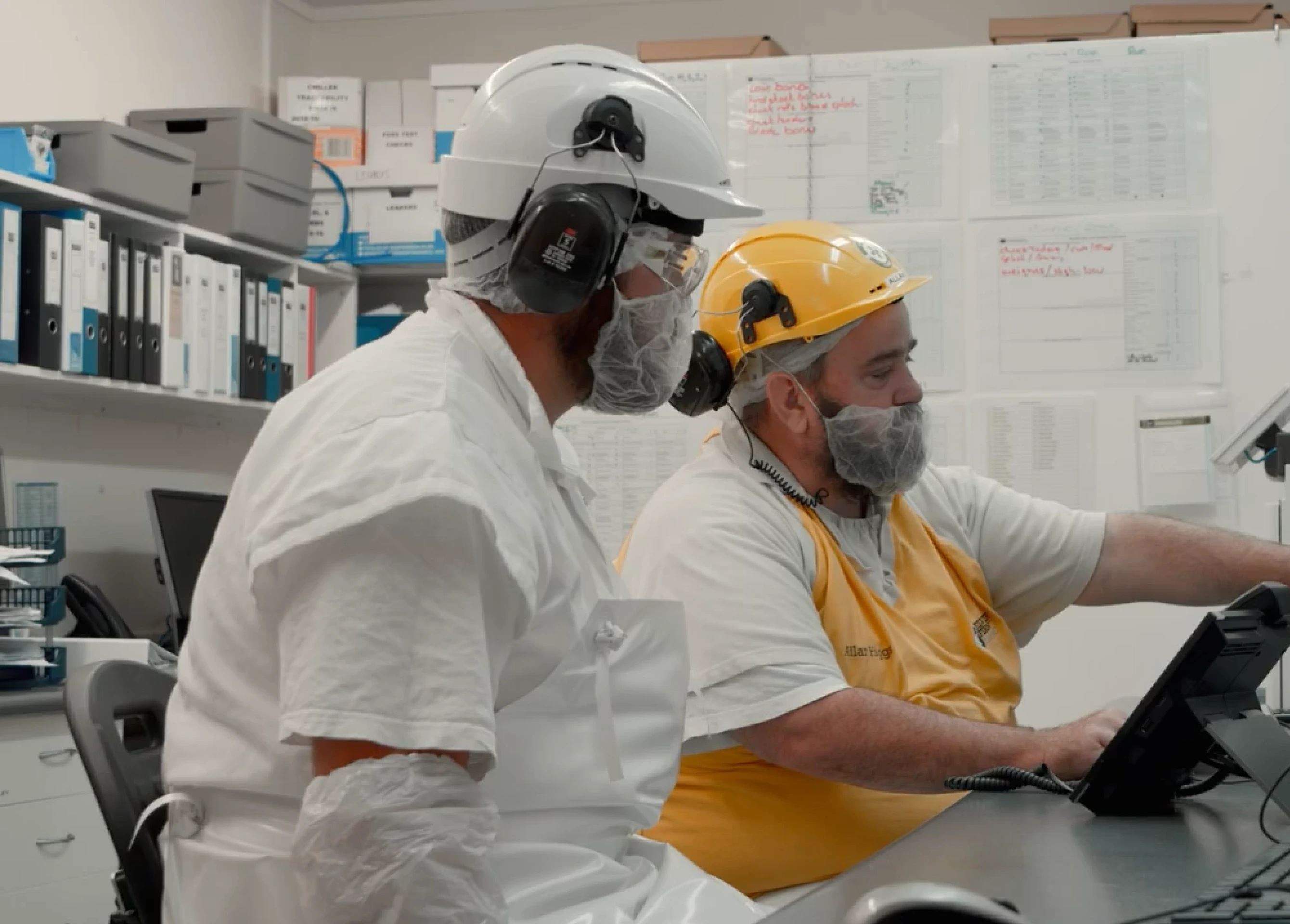
Having a reliable team of bandsaw operators can make or break a business. Unfortunately, the average retention rate of bandsaw operators is fairly low, which can be attributed to several reasons. According to one analysis of US band saw operators, approximately 40% stayed in their band saw role for less than one year, and over 30% stayed for only one to two years. So why is the retention rate of bandsaw operators so low, and what can be done to improve it?
Why does employee retention matter?
Employee retention is important to the success of an organization. It will improve morale, productivity, and revenue. Not only is it more economical to keep existing employees rather than hire new ones, but it also encourages interest in new positions. Interested candidates can see that others have stayed in their positions, and this indicates a good company to work for.
Why do bandsaw operators quit?
High risk, low reward
It’s well known that bandsaws are dangerous machines that can cause serious injury. If a bandsaw operator injures themselves on the job, or witnesses someone else getting injured, this could be enough for them to leave the company for good. It’s very important that operators feel safe while on the job, nobody deserves to be injured while working. Along with this, the average bandsaw operator generally earns below the USD national average. So, for a position that is relatively high risk and low reward, it may not incentivize workers to stay in the industry.
Lasting effects of Covid
It goes without saying that covid has had lasting impacts on almost every industry possible. And since bandsaw operators could never really work remotely, there have been ongoing issues. Many people left their jobs during the pandemic, for a different company or a completely different industry. For some, the pandemic highlighted issues they may have faced in their workplace, like poor management, working conditions, lack of safety etc. Offering the highest bandsaw safety with Guardian Bandsaws will help address workplace challenges.
Steps to improve retention of bandsaw operators
1. Improve safety
Safety is paramount when it comes to operator retention, and it’s also just good business sense. For every $1 invested in safety, there is an average ROI of $4. Simply put, bandsaw operators want to stay in a job that makes them feel safe, and one of the best ways to achieve this is with safety bandsaws.
Guardian Bandsaws, for example, are more than your standard safety bandsaw, they are a complete safety system using sophisticated blade-stopping technology and safety monitoring software. Not only will these bandsaws stop operation if they come into contact with blue gloves, but they will also alert higher management.
2. Improve training
Of course, the right equipment is the first step in shifting the safety equation, training is also integral to operators feeling adequately skilled for the job. With training, operators can improve their skills and confidence, which is likely to keep them in the job longer. Trained operators will want to stay invested in the company or their role because they feel like they add value.
3. Team-building experiences
One of the big reasons people stay in a job is because they have a reliable and supportive team around them. Team building doesn’t happen overnight, though, and often requires doing things outside the work environment. However, once a team is more unified, employees will feel like they have others to lean on and hold accountable. If one feels like they’re part of a bigger equation, they’re more likely to stay in the game, for longer.
4. Care from upper management
Care from upper management can show itself in many forms, like improved safety, bonuses, clear communication, paid time off etc. It’s not rocket science to realize that people will stay more loyal to employers who are caring and value their needs.
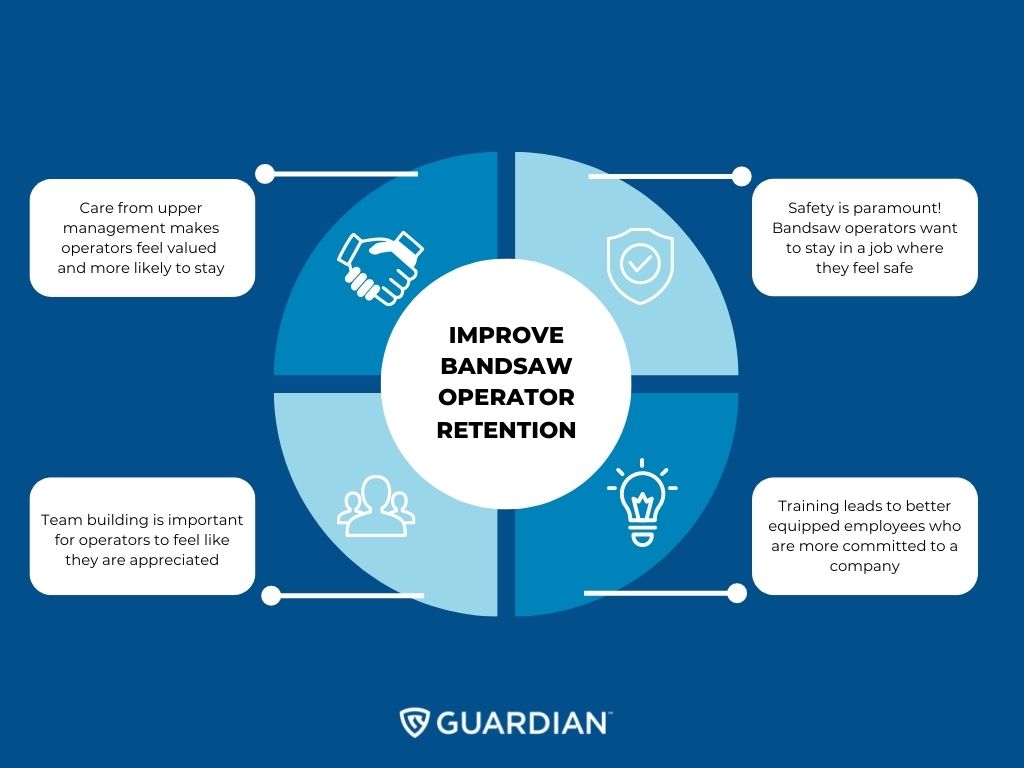
Bandsaw operator retention is something that takes a lot of careful planning and implementation to improve. It requires a combination of improved safety, training, team building, and care from upper management. However, once necessary changes have been made, the benefits are enormous. By using the data from the Guardian portal, managers can make proactive safety decisions which will help protect an operator who is operating in an unsafe or dangerous way. If you’re considering improving the safety of your operation, get in touch with the team at Guardian Bandsaw.